企業基本情報
事業者名
|
株式会社勝田容器製作所
|
---|---|
所在地
|
東京都江戸川区平井7-34-4
|
主な事業内容
|
更生ドラム缶の販売及び再生加工受託
新ドラム缶、その他容器の販売 ドラム缶更生装置設計施工 |
代表者
|
勝田幸雄
|
従業員数
|
26名
|
創業年
|
昭和21年
|
資本金
|
2,400万円
|
URL
|
エコロジーに縁の深いドラム缶再生事業
生産工程を見直すことで更なる環境配慮を実現
ISO取得をきっかけに生産現場での効率化・省エネによるコスト削減に成功
ドラム缶容器業界とエコロジー ~ドラム缶はリサイクルの優等生~
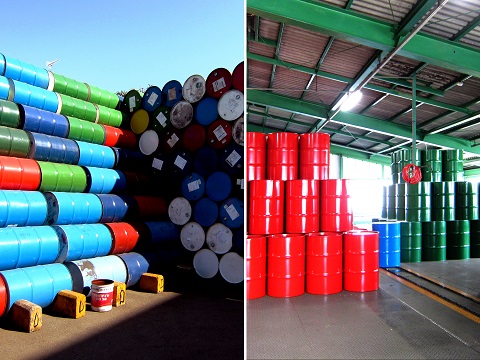
ドラム缶の歴史はおよそ110年前から始まります。1860年代にアメリカで油田が発見された後、1903年にドラム缶が発明され、気密性の点で問題があった木樽に取って代わりました。その後、2度の世界大戦による石油需要の急増に合わせてドラム缶の需要も急拡大し、生産が追い付かず再利用するしか方法がありませんでした。
わが国でも石油輸送にドラム缶は欠かせないものとなりましたが、資源に乏しい国柄、新しいドラム缶を製造する工場よりも先に、輸入した缶を修理する再生工場ができました。戦後、昭和末期まで新缶より再生缶が多くを占めていましたが、徐々に新缶が増え始め、2001年平成デフレの時代についに新缶が上回るようになりました。
現在、ヨーロッパでは板厚1mmを切るようなドラム缶が主流となったため、再利用が難しくなり再生工場はほとんどなくなってしまいました。日本においても生産コストを抑えるために新缶の薄板化が進んできましたが、耐久性や安全性を考慮して依然として板厚1.2㎜が主流となっています。わずか0.2㎜しか変わりませんが、安全性が高まるとともに、耐久性がまるで違いドラム缶は再利用率60%と高い水準をキープしています(最終的には鉄資源として生まれ変わり100%のリサイクル率)。
電気使用量の削減 ~まずはやれることから始め、徐々にレベルアップ~
省エネに本格的に取り組むことになったきっかけは、社長のトップダウンで決まった2006年5月のISO14001の取得です。まずは社内の電気を細目に消すなどやれることから取り組みました。また、工場内の作業工程を見直し、装置の運転停止時は電源を落としたりすることで、ドラム缶1本を洗浄するのに使用していた電力量は、2006年の4.4kWhから2013年には3.6kWhへと減少しました。そのほか、ドラム缶の洗浄に使用する蒸気を作るボイラーのガス使用量の削減、生産効率化も実現しました。
その後、暫く現状維持が続きましたが、2011年3月の東日本大震災が当社の省エネの取組をさらにレベルアップさせました。工場の照明のLED化を実施したところ、社員の消費電力削減の意識に再度火がつき、動力のインバータ化や手順の工夫・見直しに取り組み、2006年には400kWhあった最大電力需要量も340kWhへ引き下げることに成功。電力の基本料金が大幅に下がったことでコスト削減も達成しました。
水道使用量の削減 ~廃棄予定のタンクローリーを活用して節水~
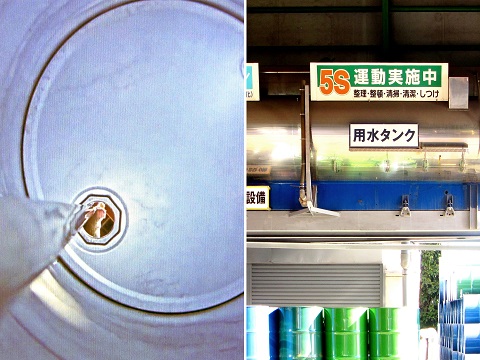
ドラム缶は、潤滑油などの石油製品をはじめ、各種ケミカル、食品油などの運搬・保管に利用されています。ドラム缶を安全かつ高品質な状態で顧客へお渡しするためには、ドラム缶の内部品質、外面の塗装品質に特に気を使う必要があります。そのため当社の作業工程では、内部・外部の洗浄、防錆などの洗浄工程で大量の水を使用します。 当社では2009年より水使用量の削減に取り組み、工場における水のリユースシステムを構築しました。以前より工場で使用した水は、用水浄化リサイクル装置により完全に浄化して再利用し一部を排水していましたが、洗浄工程の最終すすぎで使用した水は殆ど汚れが混じっていないため、浄化装置へ送る前に再利用するシステムを作りました。また、再利用するための水が余った場合は排水せざるを得ませんでしたが、貯蔵タンク(10トン)2台を設置することにより貯水しておいて後から活用することで節水することができました。 ドラム缶1本を再生するために使用していた水の量は、貯蔵タンク導入により約25%削減することができました。また、余った水を貯蔵するタンクは、実は廃棄予定だった運送事業部のタンクローリー車のタンクを再利用したもので、当社らしいユニークな試みだと考えています。
社員の意識・働き方の変化 ~ドラム缶リサイクルの「プロ職人」を説得~
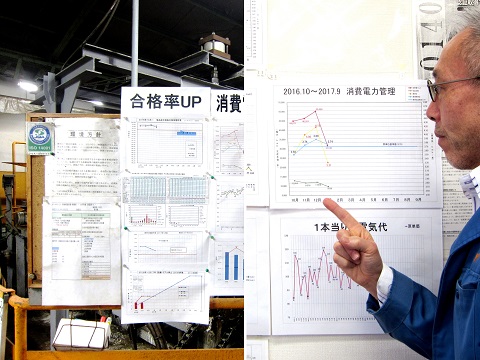
前述の通り、ドラム缶の再生事業は循環型社会の一部を担うエコ活動そのものです。それでも、2005年にISO14001を導入しようといざ省エネの実践に取り組んでみると、「原単位とは何だ?」「俺たちのやり方を変えるのか?」と言ったような声が起きるなど、社内で揉めることも多くありました。ドラム缶の再生工程は原材料が均一でないため完全自動化は困難であり、それぞれの持ち場で非常にきめ細やかな対応と知識が必要です。いわば当社で働いている社員はみなプロの「職人」なのです。そんな「職人」たちを説得し、全社員一体となって省エネに取り組むには話し合いと様々な工夫が必要でした。
その一つが電力使用量ややり直し品の削減率の「見える化」です。社員がその効果を分かりやすく実感できるように、1本の再生ドラム缶を仕上げるための電力使用量、やり直しの本数と原因などをグラフで掲示しています。今では自分達の取り組みによる成果が具体的な数値で分かるため、改善活動に自覚的に取り組んでいます。社員全員がその効果を共有し実感することが大切で、今では積極的に省エネへ取り組むことができるようになりました。そして環境マネジメントシステムの導入は「品質向上」につながりました。
メッセージ
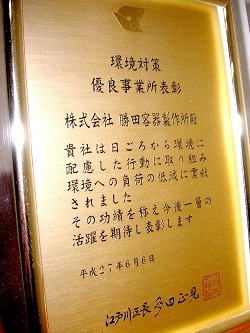
当社は法規制の遵守、雇用の安定を主な経営方針として、戦後からドラム缶の修理・再生事業を通じた社会貢献を社是としてきました。そこに今は環境保全が大きな使命となっています。
あまり知られていませんが、ドラム缶の再生は温室効果ガス排出削減に寄与しています。我々のような業者が存在しないと、新しいドラム缶を作らないといけません。そうなると、鉄板などの原材料も必要ですしその製造過程で二酸化炭素を排出します。業界でLCA(ライフサイクルアセスメント)を実施したところ、再生ドラム缶の二酸化炭素の排出量は新ドラム缶の約6分の1と算出されました。エネルギー使用量もはるかに少なくて済むのです。
環境産業と自負する当社は、自らも省エネ・省資源活動を推進するため、ISO14001の取得を目指しました。社内でドラム缶の再生作業工程に従事しているのはおよそ20名。ISO14001取得までに彼らとの衝突もありましたが、最終的には一つにまとまりました。その理由は、わが社が中小企業だからこそと思っています。中小企業は社員数が少なく、トップが会社の隅々にまで目を配ることが可能です。社長の意識と行動次第で、その気になればすぐに一つにまとまります。その結果が2015年の江戸川区「環境対策優良事業所表彰」受賞に繋がったと考えています。
日本には「もったいない」というすばらしい概念があります。地球環境に負担をかけない持続可能な循環型社会の構築のためにも、より多くのドラム缶を再生させ使っていただくことが当社の使命だと考えています。