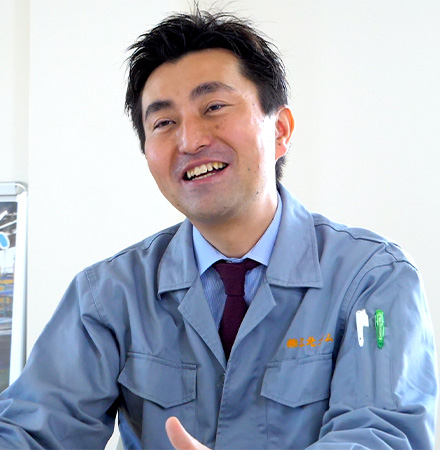
株式会社江北ゴム製作所 代表取締役社長 菅原 健太
ゴム金型製造、型成形品など、
様々な業種のニーズに対応できる
多彩かつ高度な技術が誇り。
女性活躍の環境作りなど、
人を大切にする経営が光る。
- 製造、生産管理
- 51名以上~100名以下
- 業務効率化・省人化・業務改善
- 技能伝承・脱属人化・人材育成
- ミス削減・不良率低減
- 稼働率向上・見える化(機械設備・人)
- ハードウェア(機械、タブレットなど)
- 生産管理システム、販売管理システム(製品・部品在庫管理、原価管理など)
受注から納品までの工程管理を
システム構築して効率アップ
スマートものづくり
事例MOVIE
1現場で課題と向き合う
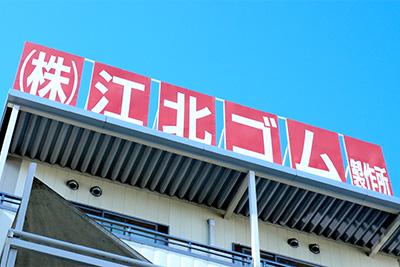
製造の段取りは工場長の頭の中のみ。
紙の管理台帳が膨大で現場は混乱
幅広い用途のゴム製品を製造する当社は、東京都内に本社と3つの工場、埼玉県に事業所、山梨県に工場(以下、富士工場)の6拠点を有しています。私は、社長就任前の10数年間、富士工場で工場長兼営業を担当していました。その当時は、中小企業によくあるように、工場のトップである私が仕事を取ってきて従業員に製品を作ってもらい、自らも現場に入る状態で、受注から納期まで一連の段取りと管理は全て自分一人の頭の中にありました。私一人で製造の段取りを組んで進めることに限界を感じ、現場の責任者に任せようとしましたが、上手く進まず悩みました。また、以前は、金型台帳をソフトウェアで管理し、受注後に金型に番号を付けて製品名や成形条件などを入力、そのデータを出力した紙の管理台帳を現場で回覧しながら工程を進めていました。しかし、「使い勝手が悪い」「紙が多すぎて分からない」などの不満の声が多く聞かれました。
当社の経営理念の中に「一生懸命が楽しく、各人の能力を高め、発揮できる会社であること」「全従業員が豊かになること」という文言があります。それらを実現するために、「もっと働きやすい仕事環境にしたい」「組織を牽引できる人を育てたい」と考えています。その想いがDX化に取り組む端緒となりました。
2スマートものづくり実践
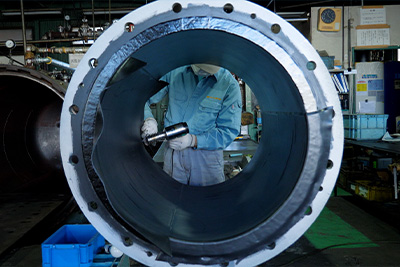
自社が使いやすいシステムによる
工程管理の実現
私は2016年に社長に就任し、仲間から情報を得て、社外の異業種交流会などに積極的に参加し、経営者同士の情報交換や悩みを相談し合う場などを活用していました。その中で、東京都中小企業振興公社の「生産性向上のためのデジタル技術活用推進事業」を知りました。当社が兼ねてから抱えていた課題の解決につながると期待し、取り組むことに決めました。
この事業では、ITの専門家が派遣されるので、当社の製造現場を理解してくれる人を条件とし、身の丈に合った進め方をしてほしいと要望しました。いくら専門家が立派なシステムの仕組みを作ってくれても使いこなすのは当社であり、自分たちが使っていく中で改良していかなくては意味がないと思います。そのためには、多少時間がかかってもしょうがないと、アドバイザーとしての役割を専門家に期待しました。
そして、この取り組みは、ゴムの金型製造から成形加工を行っている富士工場から始めることにしました。新しい仕事が増えるにつれて、金型管理方法の見直しや工程管理の効率化が必要だったからです。そこで、現場の責任者である工場長を今回のDX化の担当者にしました。工場長や管理職が頭の中で把握している工程管理を、データを用いて組織全体での管理にしていくためです。
こうして、工場長と私と専門家で進めていく体制ができ、まず、社内で現状の改善点を挙げていきました。それは自分たちの仕事を改めて見つめ直すことでもあると感じました。現場から上がってくる細かな声をシステムに反映する小さな改良は、システム会社に頼むほどのことではなく、ITが得意な知人に協力を得て進めていきました。その後も、多くの試行錯誤をしました。
システム化の着手から4年、システムを活用した、現在の当社の新たな業務フローは次の通りです。営業担当は、受注処理、成型投入計画策定のための会議、原材料の在庫引き当てと不足分の発注などをします。製造現場では、まずゴムの練り工程から始まり、出力された工程管理表にある二次元コードをスキャナーで読み取って作業を開始。1つの工程が終了したら、使用した材料などの情報をタブレット端末に入力して、次の工程へ進みます。その後、接着やプレス、仕上げ、検査の工程でも二次元コードを順次読み取ったうえで作業に着手し、終了後は各工程の情報を端末に入力します。こうした情報をデータベースで一元管理し、全社員が工程の進捗状況をリアルタイムで共有できる体制を実現しました。
現場で多かった入力への抵抗感解消のために二次元コードによる読み取り式にしました。また、工程管理表の見えにくさを解消するために大きいモニターを設置し、移動が多い作業ではタブレットを使用するなど、現場での使いやすさを重視しています。
パソコンやモニター、スキャナー、タブレットなどハード面の整備にかかった費用は約200万円で、そのうち1/2は補助金を活用しました。毎月当社を訪問していた専門家への報酬は公社が負担してくれました。最も大きいコストは社内でかけた時間や労力だと言えるでしょう。
3課題解決
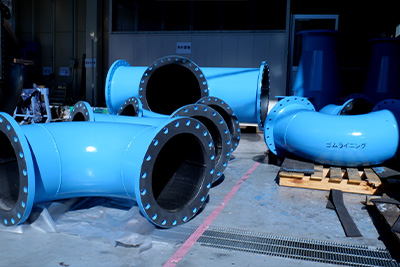
お客様に喜ばれ、
働きがいのある仕事ができる会社に
工程管理が一元化・見える化できたことで、受注処理から製造工程への作業がスムーズに進行し、今まで感覚的に分かっていたスケジュールが可視化されたので、生産効率は約2割上がったと感じています。お客様からの納期に関する回答にも迅速に対応できるなど、密なキャッチボールもできるようになり、距離が近くなったとも実感しています。お客様から感謝されるとモチベーションが上がりますし、これこそが製造業の醍醐味なので、この部分が豊かになったことも嬉しい成果です。
今後は蓄積されたデータの有効活用を目指しています。例えば、不良品や品質情報を金型管理台帳に入れて類似の不良が出ないようにするなど、当社製品の品質向上や技術の伝承に繋げていきたいです。そして、富士工場でのシステム化がひと段落したら、他の工場や事業所にも水平展開し、全社的にリアルタイムでデータを共有できる体制の実現に向けて構想しています。都内にいる営業担当がお客様から納期を聞かれて富士工場に問い合わせている現状から、システムの活用によって瞬時に営業担当自身が確認できるようになります。これは、高度な組織化を一層進めていくことでもあり、ひいては時代の変化の中でも売り上げを増加させていく基盤づくりでもあります。そして、そのシステムを使いこなして活躍できる人材を、しっかりと育成していくことにさらに注力していきます。
身の丈にあったシステム化で、使いながら改良していく。
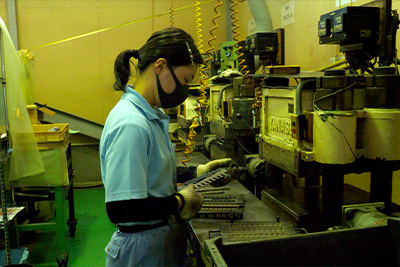
- 「働きやすくしたい」「人を育てたい」という目的があってこそのIT化が大事。昨今DXが流行っているからとか、他社もやっているからという理由で行うのは意味がない。
- 専門家に頼りすぎず、誰かから与えられたものを受け身でやるのではなく、自分たちで作り上げていく心構えと姿勢が成功の秘訣。
- 大企業でなくても中小企業でもDXはできる。ただ、焦らず、着実に。課題を一つ一つ潰しながら進めていくつもりでやっていこう。
企業情報
会社所在地:東京都足立区堀之内1-13-34、
富士工場:山梨県富士吉田市上吉田東8-1-14
電話:03-3897-4331
従業員:75名
創業:1962年
資本金:5,000万円
web:http://www.kouhoku.co.jp
2022年2月時点