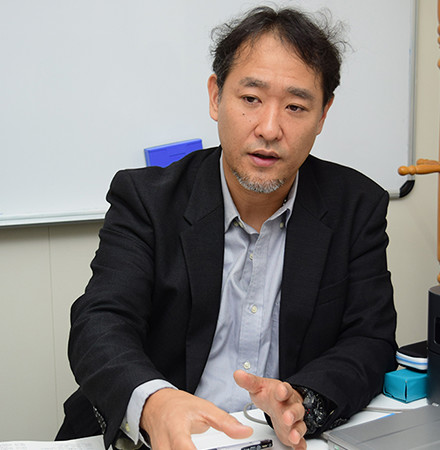
株式会社タカハシ 代表取締役 髙橋 弘明
小規模工場のIT化
システム活用からデータ分析、
FA化への道:町工場で良質な
ゴム製品を量産する製造業
- 受発注
- 製造、生産管理
- 顧客対応・営業
- 間接業務
- 5名以下
- 業務効率化・省人化・業務改善
- 技能伝承・脱属人化・人材育成
- ミス削減・不良率低減
- 品質向上
- コスト削減
- ハードウェア(機械、タブレットなど))
- 生産管理システム、販売管理システム(製品・部品在庫管理、原価管理など)
人が手掛ける仕事を明確にし、
生産性向上
スマートものづくり
事例MOVIE
1現場で課題と向き合う
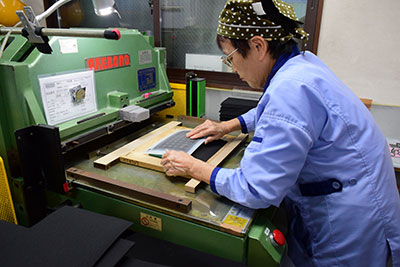
納期管理の欠如
それにより失われる信頼
30mmを超える注文書の束で、
注文や生産を管理
作業者の戸惑い、漏れる業務、
非効率な日々
当社は1948年に創業し、近年は主に自動車部品に使われるゴムパッキンを製造しています。1989年頃から自動車メーカーから部品の大量発注を受けるようになり、2006年には、取引先からの要望もありISO9001の認証取得。町工場としては、比較的早い動きだったと思います。現在は、従業員5名の町工場ながら、月産2,000万個もの商品を大量生産しています。
1997年の入社時は、注文書や帳簿は全て紙ベースでした。特に受注管理には問題があり、厚さが30mmもの束になる注文書で管理していたため、見落としや作業抜けがあり、お客様に納期調整をお願いすることもありました。進捗状況もリアルタイムでは把握できず、お客様から問い合わせを受けても、即答出来ませんでした。
また、従業員の勤務管理は紙の帳簿による手書きで行われておりました。業務がたて込む月末に、製造担当である母が半日かけて各帳簿の突き合わせ作業を行うという非効率な状況が続いていました。
2スマートものづくり実践
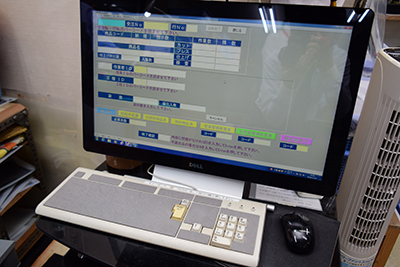
システムによる工程、
品質の一括管理へ
業務時間の大幅な削減に成功
システム構築の最初のきっかけは母が繁忙期の月末に行なっていた給与明細の作成業務の軽減でした。多くの取引先は月初、若しくはその取引先が定める締め日直後の納品を希望されます。当社にとってはまさに書き入れ時であり生産キャパも最大を迎えます。その際に帳簿の突き合わせや請求書作成といった製造とは直接関係の無い作業に半日を要しておりました。その負担は非常に大きく、お客様をお待たせする等の不具合に繋がりかねない状態でした。そこでシステム導入を検討しました。
私は学生時代にデータベースやシステムについての講義を受けた経験があり、多少の知識はありました。そこで、まずは、帳票や代表等の紙ベースの情報をエクセルなどの表計算ソフトを利用しデータ化をする試みを始めました。その後、当社現行システムのマスタの元になる生産工程の流れや帳票にどのようなことが書かれているかなどを整理しました。同時にQC工程図や品質管理体系図などの管理手法を取引先から教えていただき、システムの根幹を構築いたしました。その後、業務プロセスを見直し「より速く、正確に進めるために、システムをどのように活用すると良いか?」を目的に自社独自でマイクロソフト社アクセスを利用して簡易的なデーターベースシステムを構築しました。
しかし、システム開発と実装をすればするほど、他の業務の問題も浮き彫りになってきました。また、トレーサビリティー管理は記録類が存在せず、誰が、いつ、どこで、どのような作業をしたかの履歴が有りませんでした。顧客より要望されている管理として製品へのロットナンバーの記載があります。物品表にロットを記載するだけの簡易的な手法で、データや代表によるロットの管理も出来ていませんでした。不良品発生の原因究明時に行う、根本原因の調査も非常に苦労をしておりました。その為更なるPCシステムによる管理が必要となり受注管理、生産管理から経理に至るシームレスなシステムが必要と感じ、自社開発をやめ業務委託にての導入を決断しました。
当社では2年ほどかけて生産現場の従業員にヒアリングし、製品がどのような帳票に基づき作業が進み、流れているのかなど全ての工程を把握していきました。そのため、基本マスタ構成、工程図等の設計に必要な情報は全て揃っていました。それを元に詳細設計図はこちらで作成し、ベンダーへシステム構築を依頼しました。実はこの工程はシステム構築の際に多くの時間を費やしますが、出来る限り現状に沿ったシステム構築をする為の重要要素です。それにより現行基幹システムを製作委託したベンダー側が、当社の要件定義に割く時間とコストが削減され、構築費用はかなり低減しました。
製造現場で、特に重視したのは、「誰でも使えるものにすること」でした。当時の従業員の殆どが高齢者であったこととPCへの入力に不慣れなため、導入には時間を要しました。特にデータ入力時にキーボード又はマウスを使用する必要があり、訓練が必要でした。
“マウスを使わずにPCを操作してもらうには、どうしたら良いのか?”試行錯誤を繰り返している際、スーパーマーケットのレジに着眼いたしました。様々な作業を誰でも簡単に出来るシステムに共感を受け、「不要なキーはとってしまおう、入力はバーコードで読み取るだけにしよう」と思いつきました。バーコードリーダーを購入し、バックスペースと矢印、テンキーだけを残したキーボードを製作し入力してもらうようになりました。こうした試行錯誤を経て2008年にシステムを導入した結果、作業者が受注情報から自動で作成される作業指示書のバーコードを読み取り、数字を入力するだけで、工程管理・ロット管理をはじめ、納品書や請求書の自動出力も出来るようになりました。1時間かかっていた進捗確認も即答出来るようになるなど、様々な業務の短縮を実現しました。
3課題解決

工程の見える化で
細部に渡り正確な管理
機械と人間で
仕事を分担することで効率化
商品の製造工程が記録されると、トレーサビリティーが明確になり、不良品発生時に迅速な対応が可能となりました。特に根本原因の要因調査に関しての精度は格段に上がり、再発防止に対しても絶大な効果をもたらしました。そのほかにも、作業指示管理に割いていた業務時間が大幅に削減されましたので、お客様から受注した部品の製造に集中できるようになり、一人あたりの生産量が拡大、品質の向上にも繋がっています。材料受け入れから梱包・発送作業に至る全てのプロセスの記録を一括で管理できました。
システムを導入したことで、稼働率や個人の生産実績などのデータが蓄積できるようになりました。それにより人事評価に繋げることもできると思います。また、出勤状況はシステムの履歴でわかりますのでタイムカードの記帳を廃止しました。
また、現在ロット検査に関してはメーカーで販売している機械を使っていますが、最終的には自社開発の全数検品機導入を目指しております。画像認識のソフトを使い、大量の部品を高速で正確に検品出来るように開発しています。「コンピューターがやる仕事」と「人間がやる仕事」を明確に分け効率化を図り、品質管理と時短に繋げることを目的としています。現状に甘んじることなく、さらなる進化を目指しています。
ハードウェアの価格も手ごろに
ぜひチャレンジを!
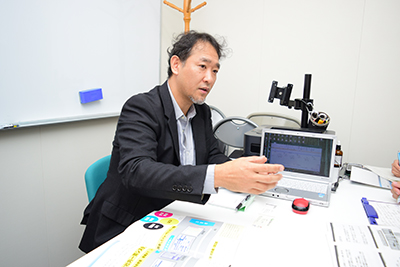
成功のカギは自社の工程を精査し、どこでどのような情報が必要になるかを洗い出すことです。それが出来ればあとはどのようなシステムを誰がどのように構築するのかといった手段の問題となってきます。その手段としてのハードとソフトがありますが、たとえば、ハード面では10年前には数万円程したバーコードリーダーが今は3千円で導入できるなど、安価になりました。また、ソフト面で言えば、自作にてデータベースが構築できる“Filemaker”が進化を進めており、より簡単に作成が出来るようになっています。
IoTやICT技術に関してもプログラム入力をする事が無く使える制御系PCがあり、誰でも簡単にソフトを構築出来る時代です。先ずは興味をもって、調べて、トライしてみることが大事です。
企業情報
会社所在地:東京都荒川区東日暮里6-3-5
電話:03-3806-5682
従業員:5名
創業:昭和23年
資本金:1,000万円
web:http://www.gomukakou.com
2019年2月時点