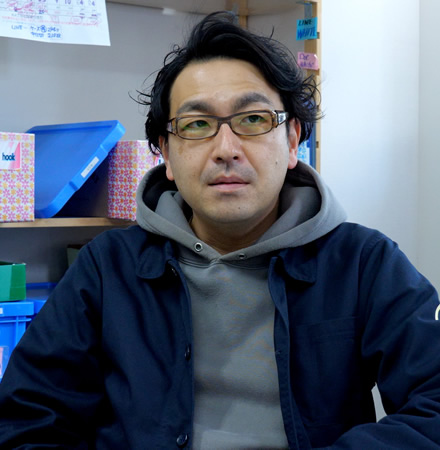
株式会社ヨシズミプレス 専務取締役 吉住 研
月産100万個のものづくりを担う。
若手が誇りを持って働ける工場へ。
- 製造、生産管理
- 11名以上~20名以下
- 業務効率化・省人化・業務改善
- ミス削減・不良率低減
- センサー・カメラ
- その他
AIを活用した検査システム導入に挑戦、
生産性の向上を実現
スマートものづくり
事例MOVIE
1現場で課題と向き合う
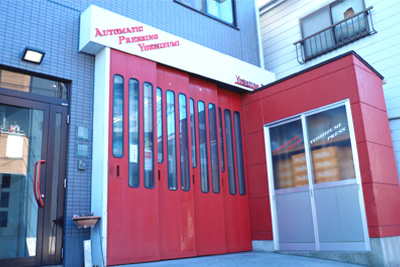
双眼顕微鏡による目視検査は
膨大な時間を要し、
スタッフはかなり疲弊
当社は金型製作から順送プレス加工までの一貫生産を行っており、電池部品や金属文具などを主に製造しています。私の祖父が足踏みプレス機1台で創業し、現社長の父は町工場のイメージを変えて若い人が誇りを持って働けるような環境作りに邁進してきました。赤を基調としたスタイリッシュな外観デザインの工場もそのひとつ。また、Automatic Pressing Yoshizumiの略称A.P.Yをロゴにしています。私は学校卒業後からこの会社に入り、父の想いを共有し、作業着ではなくロゴ入りのポロシャツを作り、名刺デザインにもこだわるなどの工夫をしてきました。
また、「ものづくりコラボレーション」「実はすみだが支えている」などのすみだ地域ブランド戦略にも積極的に参加しています。さらに、自社商品の開発を進め、「フレッシュゆめ工場」の第1期モデル工場にも認定されて、それぞれの夢を叶える「ゆめ工場」の実現を目指しています。
当社の製品のほとんどは、1つにつき10万個以上生産するものです。例えば、ボールペンのクリップは、月産200〜300万個。製品の検査も品質管理に不可欠な重要な仕事で、それぞれの製造現場の担当者が行い、プログラミングすればワンタッチで製品の規格チェックが可能な画像測定機などの検査機器も早くから導入しています。
2020年、新規の仕事が立ち上がりました。車の自動運転のセンサーに用いられる半導体レーザーの製造で、1度に30〜50万個製造する必要がありますが、国際規格がありその品質に対しては従来以上の高度な要求があります。直径5mm程度の部品で、肉眼では見えない小さな傷や変形の有無まで検査しなくてはならないため、検査担当者が顕微鏡で検品をしていました。従業員6名で約10日間を要し、心身ともにストレスの大きいこの検査業務の改善が喫緊の課題となりました。
2スマートものづくり実践
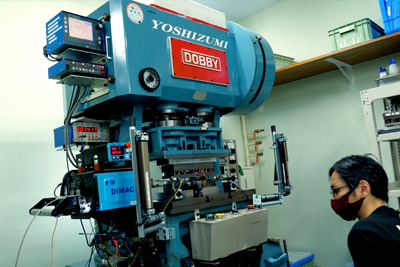
専門家のサポートで、
AIによる検査を実現。
試行錯誤して学ぶ。
行政が企画したワークショップに参加し知り合った方から教えていただいたのが、経済産業省のAI支援事業。コンサルティング会社の支援のもと、AIの知識のない当社でもできるというので、AI による画像検査の導入に取り組むことにしたのです。
ソフト面はコンサルティング会社、ハード面は当社が担当するという役割分担でスタートしました。まず、ハード面では月産50万個の製品を並べて検査するため、整列機を製作しました。これは自社倉庫内に眠っていた整列機を使って、ベルトコンベヤーで製品を1つ1つ送り出す装置を作り、試行錯誤しながら完成。社内の職人からもアドバイスがあり、ものづくりの会社の良さを実感しました。ソフト面では、AI に学習させる(=トレーニング)にあたって、良品と不良品の画像を当社が用意します。不良品は約1,000枚におよぶ様々なパターンのサンプルが必要で、実際に検査装置で使うカメラで撮影。AIのトレーニングには、スピード重視か精度重視化など細かい設定をする必要があり、当社は精度重視で調節を行い、何度もやり直してベストな設定を決めていきました。こうしたステップでは、コンサルティング会社も助言してくれますが、「なるべく自分でやってみてください」という方針なので、専門用語を覚えながら試行錯誤して学んでいきました。
整列機の製作からAIのトレーニングまで約4~5カ月かかり、20年10月から稼働を開始しました。現在、AIによる検査時間は月300時間ほど。1ロット2万個で約10時間要すため、1日2回稼働させれば4万個の検査が可能になりました。24時間フル稼働で、我々が寝ている間にこなしてくれます。準備は大変でしたが、立ち上げさえしてしまえばあとは簡単だと実感しています。今後は、さらに試行錯誤を重ねて、ブラッシュアップしていく予定です。
3課題解決
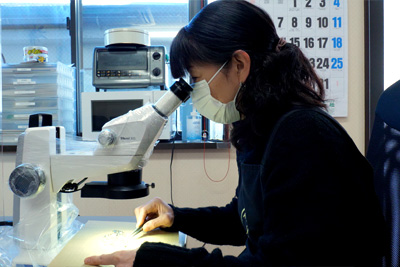
目視での検査時間が激減、
生産性が高まり利益率も向上。
AIをさらに活用していきたい。
これまで50万個の製品を6名で10日間かかっていた目視検査は、AIの導入により、総時間が1カ月につき40%減。AIが良品と判定した製品(48万個)はそのまま出荷し、不良品と判定した製品(2万個)は検査担当者が再度検査しています。つまり、50万個行っていた目視検査は2万個で済むようになり、人手のかかる業務が自動化できたことにより、従業員の負担が軽減され、利益率が向上したという成果を得ています。
今回のAI導入にかかった費用は、GoogleのAIツール利用料としての2万円と社内で整列機を製作した費用の20~30万円。コンサルティング料は、経済産業省が負担してくれる事業でした。AIというと大企業が多額の費用をかけて行うイメージがありましたが、当社のような町工場でも活用できる機会を得て感謝しています。
当社は新しいものにどんどん挑戦する社風なので、苦労を感じませんでしたが、未経験のAIを試行錯誤しながら進めていくのはある程度の時間も人力もかかることを実感しました。今後は、社内にAI人材を育成したいと考えています。勉強すれば自分たちで活用できる。そうすれば、新しいAIの仕組みも考えられる。特に生産量が多いものは、将来的にAI活用による検査が増えていくと予測し、これからも新たな挑戦をしていきたいです。
まずは挑戦することが大切。専門家のサポートで、町工場でも手軽にAIを導入できる。
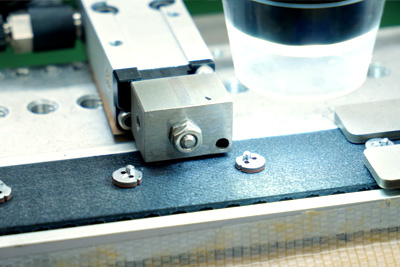
- 公的な支援事業を上手に活用すれば、費用を抑えて実行が可能。
- 専門家に丸投げではなく、教えてもらいながら自分たちが勉強して試行錯誤することで、新しい知識を身に付けることができる。
- AI導入に手間と時間がかかることは覚悟しよう。しかし、稼働後はかなり楽になる。
- AI人材を社内で育成することが将来の可能性を広げる。
企業情報
会社所在地:東京都墨田区立花4-28-2
電話:03-3612-7541
従業員:18名
創業:1950年
資本金:1,000万円
web:http://www.yoshizumi-press.com
2022年2月時点