~社内システム構築による生産業務効率化。金型管理やQRコード活用など独自の仕組みづくりも~
株式会社駒屋(本社:墨田区東駒形、社長:須藤 文雄)は、財布等の小物を中心とした皮革製品の企画・製造を行う企業です。OEMを中心に、ファクトリーブランドや写真を組み合わせたセミオーダーサービスなども展開。コロナ禍を契機に小ロット生産が主流となり、現在はほとんどの製品を国内で製造しています。
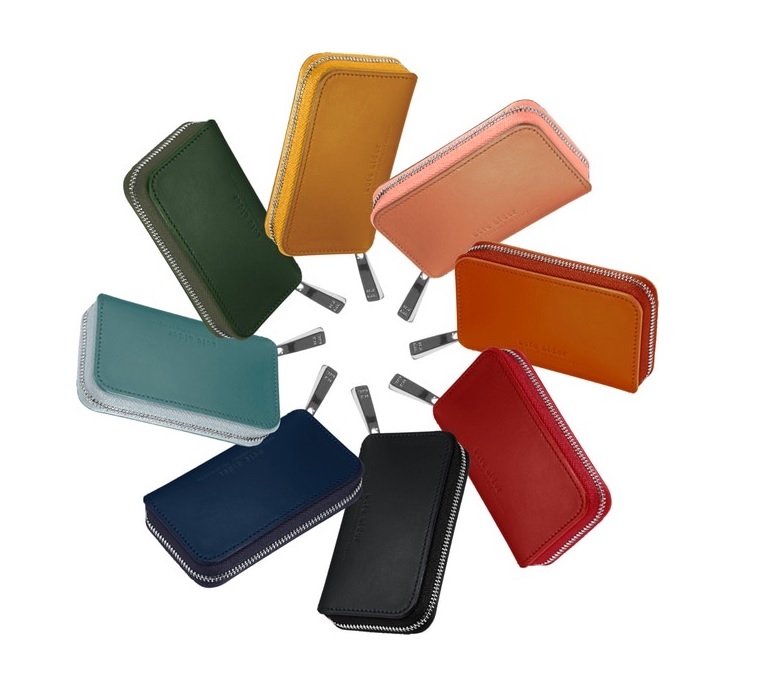
自社ブランド「acte aider(アークトエディー)」 新商品はキャッシュレス化、女性の鞄の小型化に合わせて使い勝手を考え抜いたミニ財布
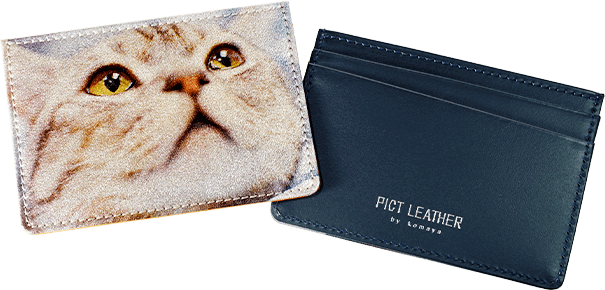
写真と革を組み合わせオリジナル製品が作れる「PICT LEATHER(ピクトレザー)」
デジタルシフトのきっかけ
海外では先進的な動きがある一方、国内産業はオートメーション化がほとんど進まず危機感を覚えていたという須藤社長。「今後人手不足が進み、ベテランの職人が退職してしまえばいずれDXに頼るしかない。デジタル技術を自分たちの業界でも活用できないか、との意識は早いうちから持っていました」と振り返ります。
また、同社取締役の西村剛史氏はデジタル業務の経験を積むため、一度はIT業界に就職。自社に戻り、あらゆる業務指示が紙で行われている状況とIT業界とのギャップに驚いた一方、「IT業界でも皮革業界でもプロジェクト工数管理の考え方はほぼ変わらないため、前職の経験を十分活かせるのでは」と考えたと言います。
デジタル活用の取り組み
現在同社では、製品設計、部材管理、見積もり、生産管理、コスト管理等に社内システムを活用し、業務効率化を図っています。なかでも特徴的な取り組みの一つが金型管理の仕組みです。 材料となる皮革を裁断するための「金型」について、約30年前のCAD・CAM導入を機に金型一つ一つのサイズ・仕様をノートに記録し続けたという須藤社長。その情報を、西村取締役が構築したITシステムに登録。画面上で形状やサイズを入力し検索すると、4万点以上のデータから適した金型がどれか、その型がどこに保管されているかがすぐに分かります。 選択した金型に必要な材料の面積情報と、使用する材料単価を掛け合わせることで自動的に見積金額を算出。材料価格が変動した場合も、システム上の価格を変更すれば見積もり等すべての関連データに自動的に反映されるため、紙で変更指示を出していた際の「見逃しによる原価への反映漏れ」「情報更新にかかるコスト削減」といった課題も解決されました。 「以前は金型を管理し切れず、受注の都度金型を仕立てることもありましたが、原材料価格が高騰した今、一から金型を作る場合は製品価格に金型代を上乗せして請求せざるを得ません。既存の金型を有効活用できれば金型製作に係る費用も抑えられ、自社にとっても顧客にとってもプラスになっています」と西村取締役。今後は金型別の利用状況や使用頻度等のデータ活用も見込んでいます。 また、生産の小ロット化が進んだことで、採算性の検証にこれまで以上の高精度な実績把握が不可欠に。そこで、本社で行う製造工程(裁断、検査仕上げ等)の実績把握のため、QRコードを活用した生産管理の運用を開始しました。 作業者は発注書に印字されているQRコードを読み取り、作業の「開始」「終了」のボタンをタップ。製造にかかった時間が記録され、計画値と実績値の自動集計と比較を可能としました。「生産能力を正確に把握するため、まずはデータを収集する仕組みづくりが先決でした。様々な年次の職人でも運用しやすいよう、『QRコードを読み取る』だけの簡単な仕組みにしました」と西村取締役は言います。 収集したデータは、 ・コスト目標と実績の差異をリアルタイムで認知し、収益改善 ・計画外業務(機械修繕、手戻り対応等)に割かれた稼働量を把握、原因特定、改善 ・工程ごとの実績を把握し、どの工程でボトルネックが発生しているかを明らかにする 等、課題を正確に見極め改善策を講じるためのツールとして前向きに活用していきたいと語ります。 なお、これらの仕組み作りの結果、特に若手社員がシステムの使い方を学ぶうちに製造業務の流れを理解していくようになり、人材育成の点でも非常に効果が表れていると強調します。
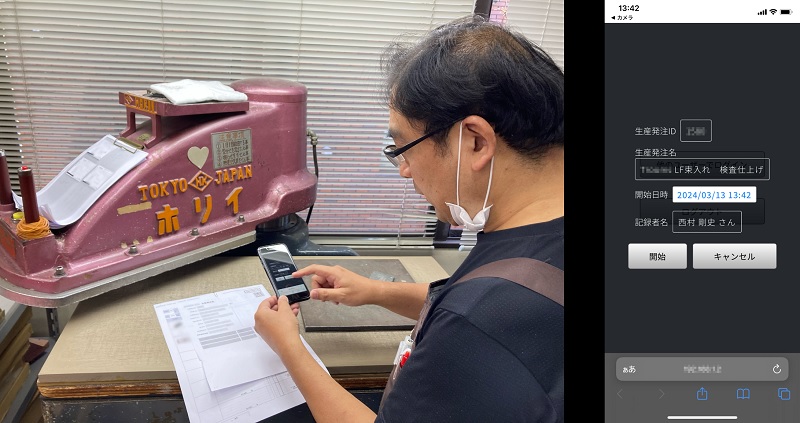
QRコードを読み取る様子
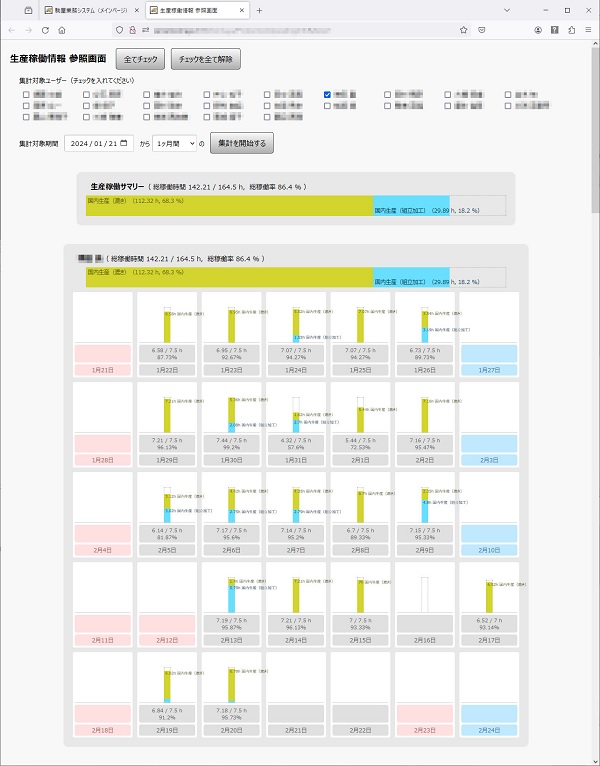
生産稼働状況が一目で把握できる
今後の展望
次のステップとして、生産計画を管理する仕組みづくりを進めたいと言います。「通常、製品の製造スパンは3~4カ月。この間の仕事の状況が分かっていないと、営業担当がどのくらい案件を受注すれば良いかの目途も立てられません。今は担当者の頭の中で行っている生産計画を仕組み化し、営業と製造の架け橋となるようなツール構築ができれば」と西村取締役は意気込みます。また、自社ブランド販売チャネルとしてEC活用も見込んでいます。
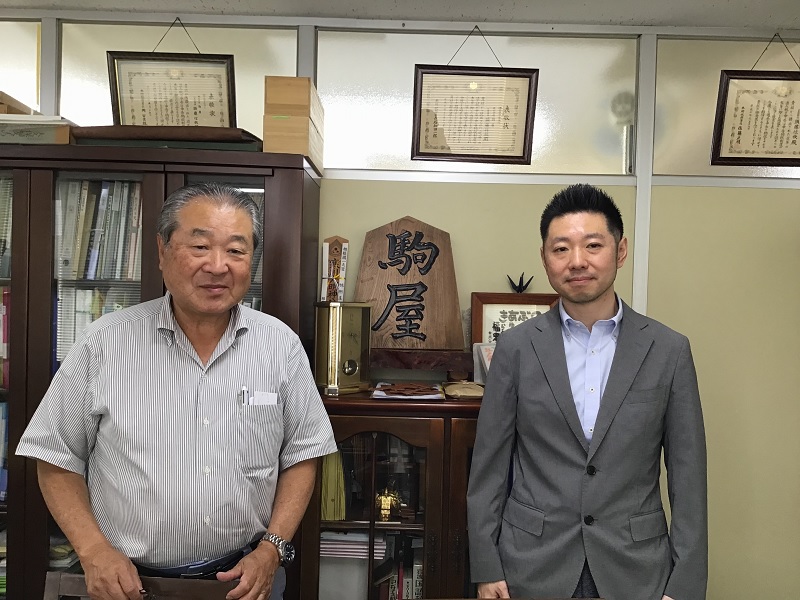
須藤社長(左)、西村取締役
ぴったりDXのTOPページは こちら