~RPA&RFIDを武器に、激化する価格競争・人手不足に対応~
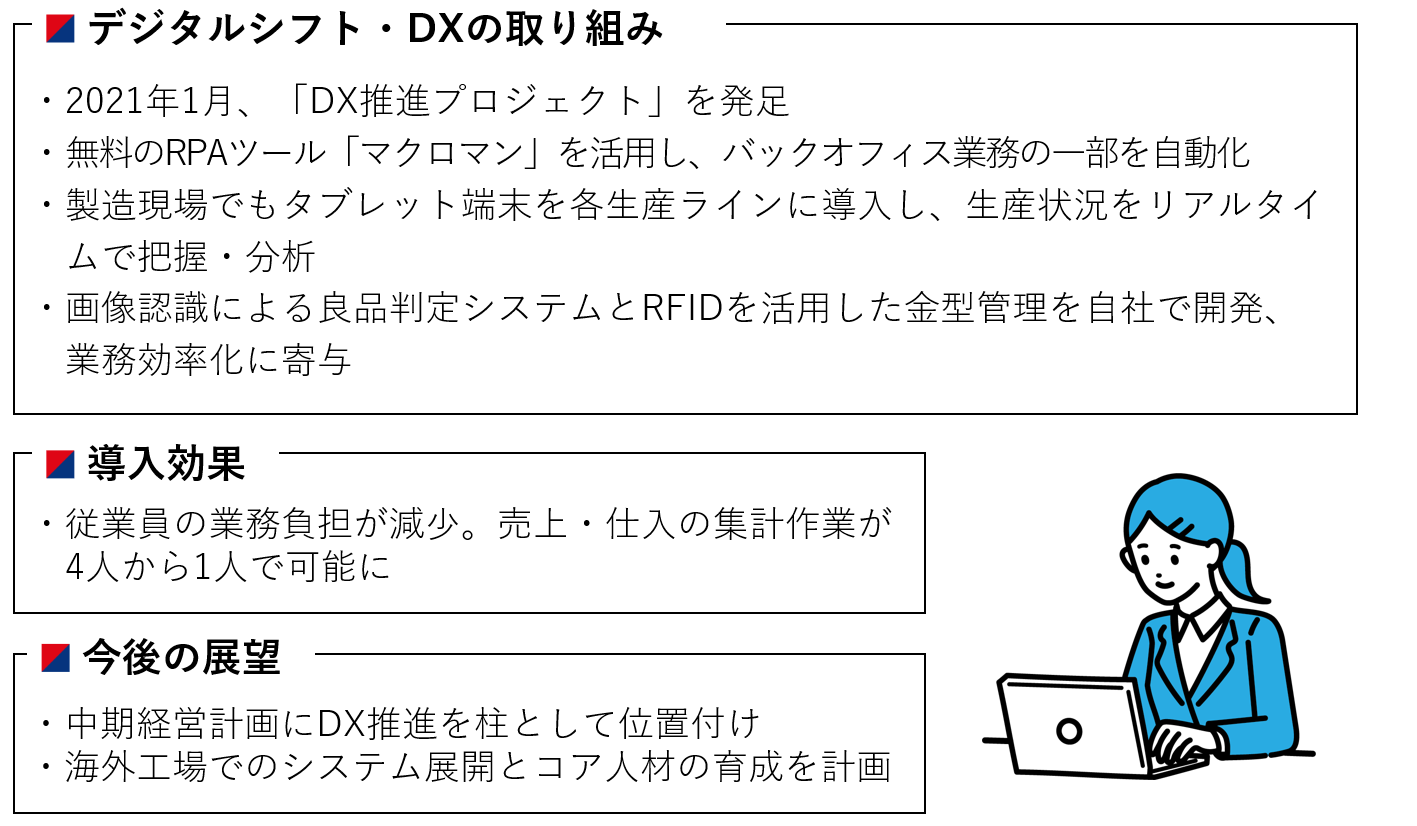
株式会社昭芝製作所(本社:練馬区小竹町、社長:三原 寛人)は、エアバッグケース、シートフレームなどの自動車部品の製造、金型の設計・製造を中心に手掛ける製造業です。
デジタルシフト・DXの取り組み
同社は、1980年代から工場のロボット化などに取り組み、IT化は以前から進めていましたが、自動車部品業界で激化する価格競争、加速する人手不足などを背景に、さらなるデジタルシフト・DXに取り組むべく、「DX推進プロジェクト」を2021年1月から社長をトップとする12人体制で発足し、同社の全社的なDX推進を本格的にスタートしました。同プロジェクトの最終目標はDXですが、まず、「デジタイゼーション」「デジタライゼーション」に取り組みます。まずは、バックオフィス業務のデジタイゼーションとして、業務の自動化と業務アプリの自社開発を行います。業務の自動化では、無料のRPA(PCの自動操作)ツール「マクロマン」を活用し、EDIシステムから受注情報を取得、自社の基幹システムに取り込み、必要な処理を自動で行い、1日累計2時間程度かけて行っていた作業を無人化しました。また、社内イントラネットシステムとして導入している「desknet's」の機能「AppSuite」を活用、特徴であるノーコードを生かし、社内申請フォームや稟議システムを自社制作しました。今まで手書きで行ってきた申請・稟議をシステム化することで、申請者・承認者の利便性が向上するとともに、データを横断検索することができるため集計作業が大幅に効率化しました。また、先述のプロジェクトメンバーが各部署で「マクロマン」や「AppSuite」を使って業務効率化に取り組んでいるとのことです。
さらに、DXプロジェクトの一環として、製造現場のデジタライゼーションにも取り組みます。生産工程において、今まで生産指示カードとして紙で出力し、作業者や作業時間、進捗をオペレーターが記入、基幹システムに入力していたものを、各生産ラインにタブレット端末を置き、情報を直接システムに入力できる体制を整えました。これによって、リアルタイムで生産実績の把握ができるようになり、ラインごとの作業時間も表示され、標準タイムに対する遅速をリアルタイムで一覧化できるようになりました。各ラインの負荷状況も色で見える化できるようになり、作業者の割り振りもしやすくなりました。加えて、画像認識による良品判定システムを自社で開発、パーツの有無判定、刻印の有無判別など、製造工程でのミスがないかを市販のウェブカメラと自社で制作したソフトウェアを使って判別しています。また、RFID(電波を使ってICタグのデータを非接触で読み書きする仕組み)を活用した金型管理を行っており、非接触で瞬時にラックの中の金型の有無を把握することができ、在庫管理・棚卸の大幅な効率化に寄与しています。
デジタルシフト・DXにあたっては、従前から情報システム部門として設置していた「IT戦略室」の体制を1名から3名体制に強化し、同室長の阿部 洋人氏が主に旗振り役となって進めてきました。阿部氏は、同社のDXを次のように語ります。「当社では、システムをできるだけ自社で開発し、コストを掛けないことを意識しています。また、外部研修や社内講習会等の実施により、従業員(システムの使い手)の育成も積極的に取り組んでいます」
効果と今後の展望
デジタルシフト・DXを進めてきた効果として、従業員の業務負担が確実に減っており、例えば、売上・仕入の集計作業を行う担当は従来4人で行っていたものがシステム化により1人でできるようになったといいます。
現在では、中期経営計画でも柱の1つ目にDX推進を位置付けている同社ですが、今後の展望として、システム標準化とあわせて海外工場での展開、海外工場で旗振り役となるコア人材の育成、サイバーセキュリティ対策の強化をしたいといいます。
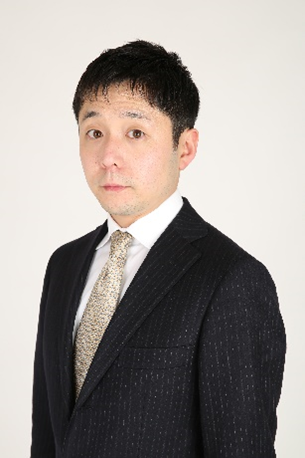
三原社長
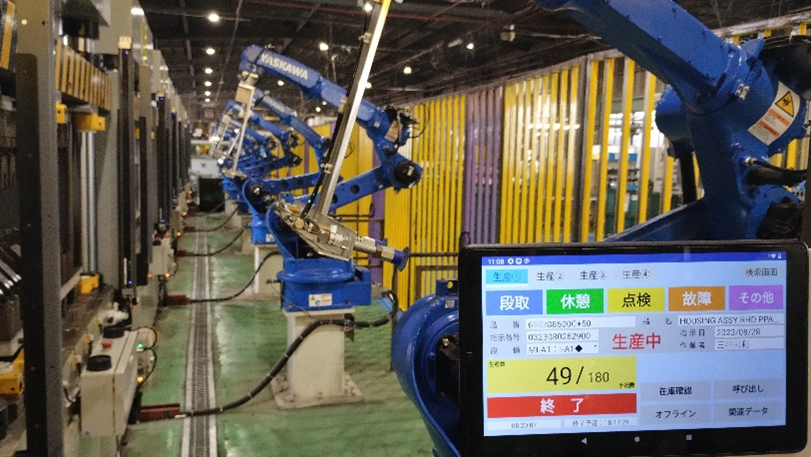
工場のロボット化・タブレット活用の様子

- 所在地
- 練馬区小竹町1-43-15
- 代表取締役
- 三原 寛人
- 設立
- 1961年
- 業種
- 製造業(エアバッグケース、シートフレームなどの自動車部品の製造、金型の設計・製造等)
- 従業員数
- 101名
- URL
- https://www.shoshiba.co.jp/
ぴったりDXのTOPページは こちら