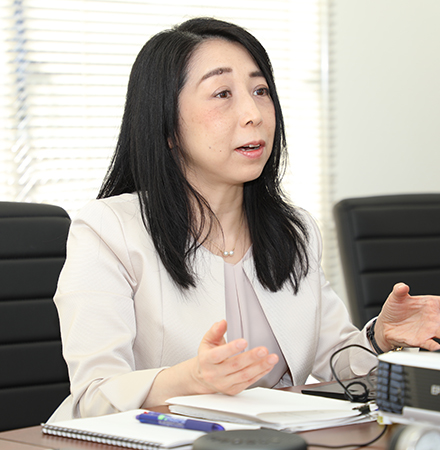
山本計器製造株式会社 代表取締役社長 山本 直子
社会インフラの一端を担う
創業80年の計器メーカー
- 製造、生産管理
- 会議、情報共有
- 51名以上~100名以下
- 業務効率化・省人化・業務改善
- 技能伝承・脱属人化・人材育成
- コスト削減
- 生産管理システム、販売管理システム(製品・部品在庫管理、原価管理など)
職人・技術者の記憶やノウハウを
データ化することにより、
製品の部品情報を共有化し迅速対応を実現
スマートものづくり
事例MOVIE
1現場で課題と向き合う
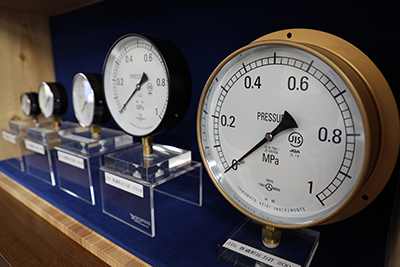
どの部品が必要になるのか。
知識の属人化が課題
当社は圧力計と温度計のメーカーで、製品は大きなビルの空調の配管、駅ビル、病院、水族館など実に様々なところで使用され、圧力や温度の管理を支えています。一見シンプルに見える計器ですが、JIS規格対応や、計測対象の物質、取り付けられる場所などにより製品は多種多様で、汎用品もあれば特注品もあり、受注頻度の高いものもあれば年に1回しか売れないものもあります。それぞれの製品に対応するケース、カバー、目盛板、針、ネジなど必要な部品の種類は3千~4千にも及びます。
製造は岡谷工場で行っており、顧客の発注内容をもとに営業担当が仕様を文章にし、そこからさらに製造に必要な情報を工場で読み解いて、各部品の材質やサイズ等を判断して部品の調達と組み立てを行ってきました。こうした部品の管理と手配は購買のベテラン3人が担当していますが、彼らの記憶の中で管理されている状況。ところが、ある時担当者が体調を崩して休み、営業からの納期の問い合わせに必要な部品の在庫状況などがわからず現場が困ったことがあり、対策を講じることになったのです。そこで、部品管理を共有する取り組みを始めることにしました。
2スマートものづくり実践
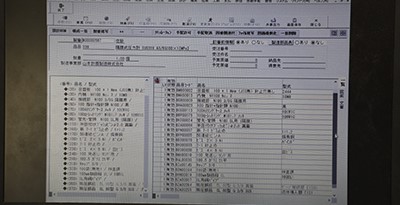
コツコツとデータを蓄積し、
システムに愛称をつけて親近感を覚える
まずは工場でA3サイズの紙による汎用品の部品表を作成。圧力計の汎用品は約300種類以上あり、それら全てに必要な部品を約30種類を全部書き込む大きなリストでしたが、それを他の製品にも展開しないと誰もがわかるものにはなりません。現場で実際に使えるようにするためには、さらに膨大な部品の種類と数の管理になるので、システムを導入することにしました。2018年のことです。
このプロジェクトは、工場のメンバーや本社の経理・人事も担当している総務課長など7、8名でスタート。まず半年くらいかけてシステムを選び、生産管理と販売管理がセットになっているパッケージソフトを購入しました。このシステムに親しみやすいよう愛称をつけ、部品の在庫管理や購買管理の機能にまず着手。当社では1日40~50件の新規受注データが入ってくるので、その都度その製造に必要な部品情報を入れていき、データの蓄積を進めていきました。
工場では忙しい中、部品などを一番よくわかっている部門の責任者が自分の本来の仕事に加えデータの登録も担ってくれています。システム化を始めて2年経った現在、データはまだ蓄積中ですが7、8割はできてきて、部品によっては購買管理をそのシステムで管理できるところまできました。従来は部品の現物と手書きの受払カードという用紙で在庫管理していたので、大きな進歩です。
3課題解決
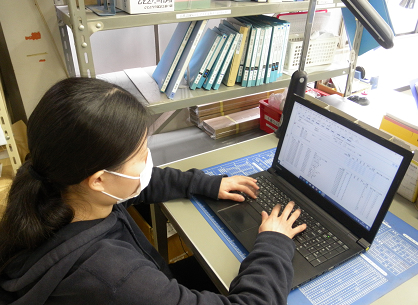
部品管理の共有化にとどまらず、
業績などを見える化
システム導入により、担当者がいないと部品管理はわからないという状況は改善できました。どの製品にどの部品を使うかというデータが蓄積され、担当者以外でも対応が可能になりました。使用箇所や使用頻度の多い部品、短納期に対応する部品、製作に長期間かかる部品などは欠品しないように、在庫に着目した安全在庫数という数字を設定管理できるようになったので安心して受注できます。新規注文の場合、原価の問い合わせが営業から来ますが、今までは購買3人がそれぞれに担当する部品の原価を調べてもらうのに2、3時間かかっていたものが今では5分もかからずに回答できます。納期回答も同様で、製造段階で受注数に対応できるか部品があるかがわかるのですぐに納期を算出することも可能になりました。
また、営業も工場もコスト意識が変わったと思います。今までは購買の担当者任せだったので部品の正確な原価を共有することが難しかったのですが、システムによって部品1個の原価もすぐにわかるので、利益率を考え販売することの大事さも実感できるようになりました。
さらに経営面で言えば、仕入れや在庫の金額が容易に把握できるようになったため、少なくとも2カ月先までのキャッシュフローを見通すことができ、また、原価の把握を通じて月次で業績を捉えることができるようになりました。
今後は、残りの2、3割のデータを完成させていくことを目指し、いずれは部品だけでなく工数の原価や管理までできるようにしたいと考えています。そして、パッケージソフトに備わっている機能を見極めてさらに活用していきたいと考えています。
風通しのよい環境が可能性を高める
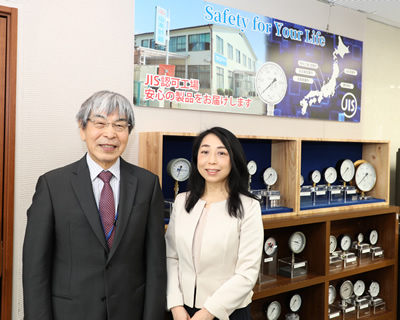
私が父(現・会長)の後を継いで社長に就任したのは2020年6月。その3年ほど前に入社した時からこのプロジェクトを進めてきましたが、周りの社員にわからないことはすぐに聞く、何でも相談しあって進めていくことを心がけています。私を通して会社のいろいろなコミュニケーションがスムーズに行けば嬉しいですし、岡谷工場ともオンライン会議などでコミュニケーションを密にとっています。風通しのよい会社であれば現場などから様々な意見が出やすく会社の改善に活かしていけると思います。
今回のシステム化にあたり、通常の業務と並行して行うのは大変ですが、ベテランの記憶やノウハウをきちんとデータ蓄積することは会社の知的財産づくりであり、世代交代をしても継承できる貴重な知識の宝庫と言えるでしょう。
企業情報
会社所在地:東京都新宿区南元町13-11
電話:03-3354-8611
従業員:70名
創業:1941年
資本金:3,000万円
web:http://www.yamamotokeiki.co.jp/
2021年2月時点